Types of production processes for stainless steel flanges
Stainless steel flange is an important component for connecting pipelines and equipment. It has the characteristics of high temperature resistance, corrosion resistance and good sealing. Common stainless steel flange production processes are mainly divided into four types: forging, casting, cutting, and rolling.
(1) Cast stainless steel flange
The process of injecting molten steel into the mold to cast stainless steel flanges is called the casting method. The advantages are: accurate shape and size of the blank, small processing volume, low cost, and the mold can be adjusted according to customer needs to produce more complex shapes. Disadvantages: Casting defects (pores, cracks, inclusions), poor streamlined internal structure of the casting, poor shear force and tensile force. Of course, there are also higher cast stainless steel flange processes that can reduce such shortcomings. For example, centrifugal stainless steel flanges are a type of cast stainless steel flanges. The centrifugal method is a precise casting method for producing stainless steel flanges. The stainless steel flanges cast in this way are much finer than ordinary sand casting preparations, the quality is much improved, and it is less prone to problems such as pores, cracks, and trachoma. The following is a detailed explanation of the centrifugal casting of stainless steel flanges.
(2) Forged stainless steel flange
Forged stainless steel flanges generally have lower carbon content than cast stainless steel flanges and are less likely to rust. The forgings have good streamlines and a denser structure. Their mechanical properties are better than those of cast stainless steel flanges and they can withstand higher shear forces and tensions. Extension.
Common forged stainless steel flanges are forged and forged.
Forged flange is a flange formed by hot processing of metal materials and then beating. The main feature of this process is to use high temperature and high pressure to gradually deform the metal material so that its shape and performance are optimized.
The difference between forged flange and forged flange is that it uses mechanical operation to mold metal materials, a metal processing process similar to that of forged flange. This process is related to forging deformation rather than manual forging.
The following is a detailed explanation of forged stainless steel flanges and forged stainless steel flanges.
(3) Cut stainless steel flange
Directly cut out the flange's inner and outer diameter and thickness disks on the stainless steel medium plate, and then process the bolt holes and water lines. The size of stainless steel flanges cut and produced generally does not exceed DN150. If the size exceeds DN150, the cost will increase significantly.
(4) Rolled stainless steel flange
The process of cutting stainless steel medium plates into strips and then rolling them into circles is mostly used in the production of some large stainless steel flanges. After successful rolling, it is welded, then flattened, and then the waterline and bolt holes are processed. Because the raw material is medium plate, the density is good. The welding process at the interface of the rolled flange is a top priority, and X-ray or ultrasonic film inspection is required.
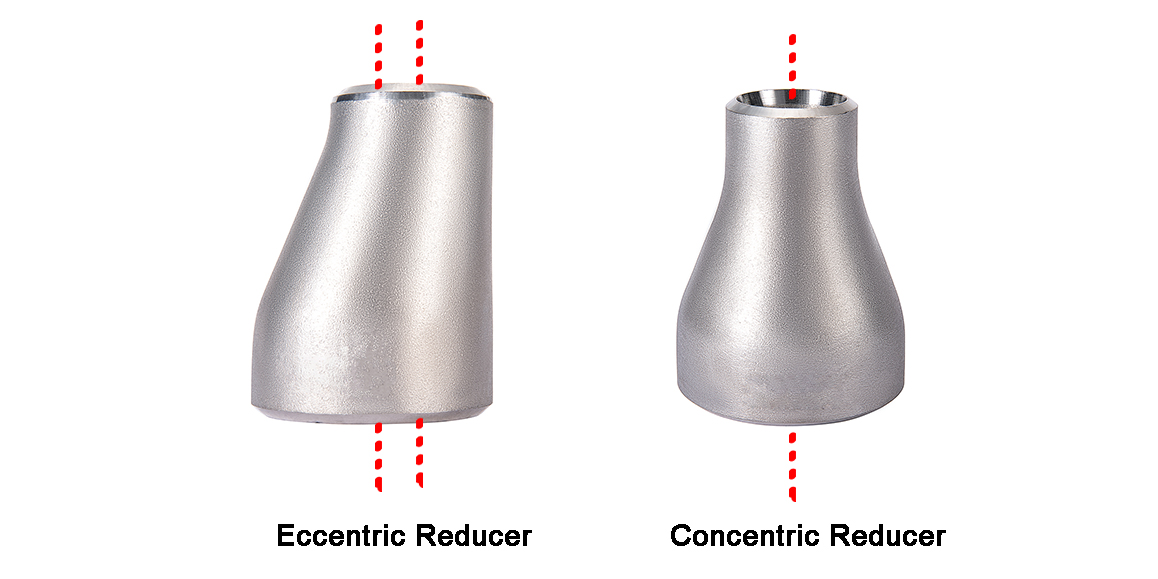
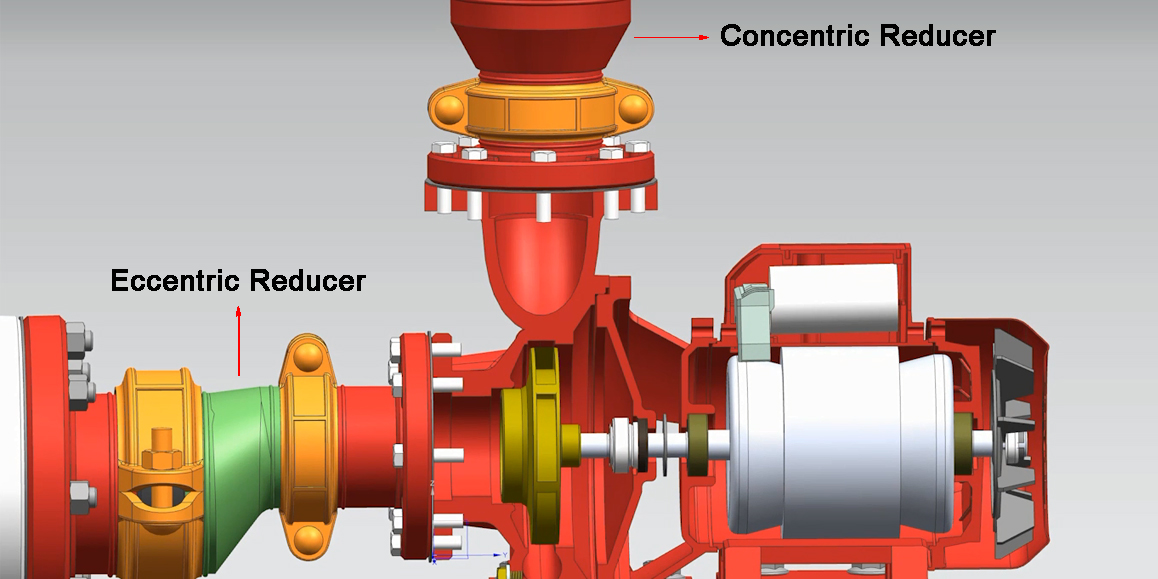